셀투바디(CTB)와 셀투섀시(CTC) 기술은 전기차 배터리 통합 방식에서 가장 주목받는 혁신 중 하나로, 전기차 설계와 성능에 큰 변화를 가져오고 있습니다. 이 글에서는 두 기술의 차이점과 특징, 그리고 전기차 산업에 미치는 영향을 자세히 살펴보겠습니다.
전기차 배터리 기술의 진화는 단순히 에너지 밀도를 높이는 것을 넘어, 차량 설계의 근본적인 변화를 이끌고 있습니다. 셀투바디와 셀투섀시는 이러한 변화의 중심에 있는 기술로, 각각 배터리를 차량의 바디와 섀시에 통합하는 방식을 채택하고 있습니다.
CTC 기술은 배터리셀(Cell)을 차량 섀시(Chassis)와 통합하는 기술입니다. 배터리 팩을 별도의 모듈로 구성하는 기존 방식과 달리, 배터리셀을 섀시 구조의 일부로 설계하는 접근법입니다.
CTB와 차이점은 CTB는 배터리가 차체의 일부가 되는 반면, CTC는 배터리가 차량 섀시와 통합된다는 점입니다. CTC는 CTB보다 차량 하부 강성에 더 직접적인 영향을 미칩니다.
셀투바디: 배터리와 바디의 완벽한 통합
셀투바디(Cell-to-Body, CTB) 기술은 배터리 셀이 차량의 바디 구조와 직접 통합되는 방식입니다. 기존에는 배터리 팩이 별도의 독립된 구성 요소로 차량 하부에 장착되었지만, CTB 기술은 이를 차량 바디의 일부로 설계합니다.
BYD는 2022년 자사의 SEAL 모델에 CTB 기술을 처음으로 적용했으며, 이 기술을 통해 배터리 팩의 볼륨 활용률을 66% 증가시켰습니다. 또한, 차량 구조 강성은 기존 대비 100% 향상되었으며, 충돌 안전성도 50% 개선되었습니다. 이러한 혁신은 전기차가 더 가볍고 안전하며 공간 효율적인 설계를 가능하게 합니다.
CTB 기술의 주요 특징은 다음과 같습니다:
- 구조적 강성 향상: CTB 방식으로 설계된 차량은 비틀림 강성이 70%, 굽힘 강성이 57% 증가해 주행 안정성과 승차감을 크게 개선합니다.
- 공간 활용도 증가: 배터리가 바디와 통합되면서 불필요한 공간 낭비를 줄이고, 내부 공간을 더 넓게 사용할 수 있습니다.
- 제조 비용 절감: 부품 수가 줄어들고 조립 공정이 단순화되어 제조 비용이 절감됩니다.
셀투섀시: 섀시와 배터리의 융합
셀투섀시(Cell-to-Chassis, CTC) 기술은 배터리 셀이 차량 섀시와 직접 통합되는 방식입니다. 이는 CTB와 유사하지만, 통합 대상이 바디가 아닌 섀시라는 점에서 차이가 있습니다.
CATL은 2025년까지 CTC 기술을 상용화할 계획이며, 이를 통해 전기차 주행거리를 최소 800km까지 늘릴 수 있다고 밝혔습니다. 또한, CTC 기술은 모터와 고전압 모듈 등 다른 주요 부품과도 통합될 예정으로, 전기차 설계의 새로운 표준을 제시하고 있습니다.
CTC 기술의 주요 특징은 다음과 같습니다:
- 설계 유연성 강화: 배터리가 섀시에 직접 통합되면서 차량 설계의 자유도가 높아집니다.
- 효율성 극대화: 별도의 배터리 팩이 필요 없으므로 무게와 공간을 줄이고 에너지 효율성을 높일 수 있습니다.
- 비용 절감: 제조 공정이 단순화되고 부품 수가 줄어들어 생산 비용이 감소합니다.
CATL은 CTC 기술을 통해 전기차가 내연기관 자동차와 비용 경쟁력을 갖추는 데 기여할 것으로 기대하고 있습니다.
CTB와 CTC의 차이점
두 기술은 모두 배터리를 차량 구조에 통합하는 방식이지만, 적용 범위와 목적에서 차이가 있습니다. 아래 표는 CTB와 CTC의 주요 차이를 정리한 것입니다.
구분 | 셀투바디(CTB) | 셀투섀시(CTC) |
통합 대상 | 차량 바디 | 차량 섀시 |
주요 특징 | 구조 강성 및 충돌 안전성 향상 | 설계 유연성과 공간 효율성 강화 |
적용 사례 | BYD SEAL, 테슬라 모델 Y | CATL 개발 중 (2025년 상용화 예정) |
장점 | 내부 공간 활용도 증가, 제조 비용 절감 | 무게 감소 및 주행 거리 증가 |
기술 논리 | 프로 | 단점 | |
CTP | 셀 배터리 팩 (대형 모듈) | 배터리 팩의 체적 에너지 밀도 및 질량 에너지 밀도를 개선하여 비용을 절감 | 배터리 셀의 일관성에 대한 요구 사항이 높고 배터리 셀을 수리하고 교체하기가 어렵습니다. |
CTC | 셀 섀시 | 자동차의 Z 축 공간을 늘리고 배터리 수명을 개선하며 비용을 줄입니다. | 통합 수준을 개선 할 여지가 여전히 많으며 배터리를 수리하고 교체하기가 어렵습니다. |
CTB | Cell | 자동차의 Z 축 공간을 늘리고 배터리 수명을 개선하며 비용을 줄이며 신체 강성을 개선하며 안전 및 취급을 개선합니다. | 통합 개선의 여지가 여전히 남아있다 |
셀투바디와 셀투섀시가 전기차 산업에 미치는 영향
이 두 기술은 전기차 산업에 다양한 긍정적인 영향을 미치고 있습니다:
1. 주행 거리 증가: 무게 감소와 에너지 밀도 향상을 통해 전기차의 최대 주행 거리가 늘어납니다.
2. 제조 효율성 향상: 부품 수 감소와 조립 공정 단순화를 통해 생산성이 높아지고 비용이 절감됩니다.
3. 안전성 강화: 구조적 강성과 충돌 안전성이 개선되어 승객 보호 능력이 향상됩니다.
4. 환경 친화적 설계: 경량화된 구조로 에너지 소비를 줄이고 지속 가능성을 높입니다.
특히 BYD는 CTB 기술을 통해 자사의 SEAL 모델에서 CLTC 기준 최대 700km 이상의 주행 거리를 제공하며, CATL은 CTC 기술로 최소 800km 이상의 주행 거리를 목표로 하고 있습니다.
셀투바디(CTB) 기술의 OEM 납품 방식: 통합 구조체로서의 혁신
셀투바디 기술의 납품 단위: 구조적 통합 모듈
셀투바디(CTB) 기술은 배터리 셀을 차량 바디와 직접 통합하는 방식으로, 기존의 별도 배터리 팩 개념을 완전히 재정의합니다. OEM(완성차 제조사)에는 통합 구조체 형태로 납품되며, 이는 배터리 셀과 차체 프레임이 일체화된 모듈 단위로 공급됩니다. 예를 들어, BYD의 SEAL 모델은 LFP 배터리 셀을 차체 하부에 직접 배열하여 82kWh 용량을 구현했으며, 이는 바닥면 전체를 하나의 배터리 모듈로 활용한 사례입니다.
공급 방식의 세부 특징
1. 맞춤형 설계 협업: 배터리 제조사(CATL, BYD 등)는 OEM과 공동으로 차체 구조를 설계합니다. 예를 들어, CATL은 2025년 출시 예정인 셀투섀시(CTC) 기술에서 배터리 셀을 섀시 프레임에 직접 통합한 모듈을 제공합니다.
2. 모듈화된 구조체 단위: 납품 단위는 일반적으로 전체 바디 플로어 섹션으로, 길이 2m 이상의 대형 블록 형태입니다. 샤오미 SU7의 경우 BYD와 CATL이 각각 다른 사양의 셀투바디 모듈을 제공하며, 이는 차체 조립 라인에서 즉시 장착됩니다.
3. 표준화 vs. 맞춤형: 중국 기업들은 특정 OEM에 최적화된 모듈을 개발하는 반면(예: BYD의 블레이드 배터리), CATL은 유연한 설계 플랫폼을 통해 다수 OEM에 대응합니다. 테슬라의 4680 배터리 통합 섀시는 미국 OEM에 특화된 사례입니다.
납품 프로세스 및 비용 구조
- 공정 단순화: 기존 200~300개의 부품으로 구성되던 배터리 팩 대신, CTB 모듈은 10개 미만의 주요 구성품으로 제조됩니다. 테슬라 모델 Y의 경우 부품 수 370개 감소, 제조 단가 7% 절감 효과를 달성했습니다.
- 물류 효율성: 모듈 당 평균 500kg의 무게를 가지며, 8~12개의 대형 모듈이 한 대의 차량에 납품됩니다. 이는 기존 팩 대비 물류 비용을 20% 이상 절감시킵니다.
산업 구조 변화: 파운드리 모델의 부상
배터리 기업들이 전기차 파운드리로 진화하며, 완성차 업체에 배터리-차체 통합 모듈을 공급합니다. CATL은 2024년 기준 6개 OEM과 파운드리 계약을 체결했으며, 배터리 통합 섀시를 연간 50만 대 규모로 생산 중입니다. 이는 반도체 파운드리와 유사하게, OEM이 설계만 제공하면 배터리 업체가 통합 생산하는 형태입니다.
글로벌 사례 비교
- 중국: BYD는 자체 OEM에 연간 150만 대 규모의 CTB 모듈을 공급하며, 외부 판매 비중은 30%입니다.
- 미국: 테슬라 텍사스 공장에서 4680 셀 기반 CTB 모듈을 생산, 모델 Y에 적용하며 14% 주행거리 향상을 달성했습니다.
- 유럽: 폭스바겐 MEB 플랫폼은 590 모듈 표준을 사용하나, CTB 전환을 위해 CATL과 협업 중입니다.
기술적 과제와 전망
CTB 모듈의 교체 비용은 차량 가격의 40% 수준으로, 보증 기간 이후 유지보수 이슈가 남아있습니다. 그러나 LFP 배터리의 높은 수명(사이클 4,000회 이상)으로 인해, 10년 이상 사용 시나리오에서 경제성이 입증되고 있습니다 2025년까지 CTB 적용 전기차는 글로벌 시장의 35% 점유율을 차지할 것으로 예상됩니다.
이처럼 셀투바디 기술은 배터리와 차체의 경계를 허물며, OEM-배터리 업체 간 협력 관계를 재편하고 있습니다. 단순 부품 공급을 넘어, 통합 모빌리티 플랫폼으로의 진화가 핵심입니다.
다녀가신 흔적은 아래의 하트 모양의 공감 (♥)을 눌러서 남겨주시길 부탁드립니다.
로그인하지 않으셔도 공감은 가능합니다.
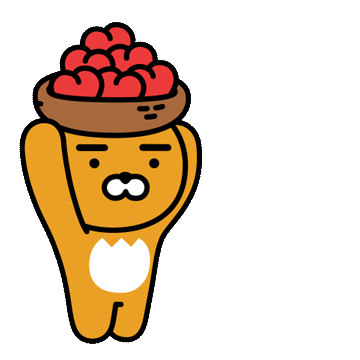
감사합니다 !
'전기차 세부 기술' 카테고리의 다른 글
CATL 베드락 롤링 섀시의 혁신이 전기차 산업에 미치는 파장 (0) | 2025.04.03 |
---|---|
LFP 배터리: 고밀도 양극재가 새로운 경쟁력의 열쇠 (1) | 2025.04.02 |
테슬라의 배터리 선택: LFP와 NCM 배터리 수명과 보증 거리의 진실 (1) | 2025.04.01 |
BYD Blade 각형셀과 테슬라 4680 원통형 셀의 설계 및 성능 비교 분석 (1) | 2025.03.26 |
테슬라 드라이 캐소드 4680 배터리와 사이버트럭 테스트의 현황과 전망 (0) | 2025.03.24 |