최근 BYD는 CTB 기술을 출시했습니다.
우리가 이미 알고 있는 CTC 기술과 비교했을 때 CTB 기술의 장점은 무엇인지 비교를 해보겠습니다.
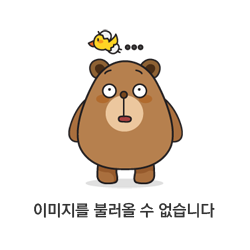
1. 배터리 시스템 개발 트렌드
"셀-모듈-배터리 팩"(일반적으로 소형 모듈이라고 함)의 형태를 추가하는 가장 큰 장점은 더 나은 관리와 애프터서비스 등 후속 유지 관리가 유용합니다.
그러나 직렬로 연결하려면 필연적으로 많은 수의 케이블과 구조 부품을 사용하여 연결해야 하며, 여기에는 많은 중복 구조가 있어 배터리 팩의 활용률을 떨어뜨릴 뿐만 아니라 전체 전원 배터리를 매우 부피가 크게 만듭니다.
위의 문제를 해결하기 위해 업계에서는 "CTP"라는 개념을 제안하기 시작했습니다. 즉, 모듈 수를 생략하거나 줄이고 셀을 배터리 팩에 직접 배치하는 것입니다. 예를 들어 BYD의 블레이드 배터리는 그 중 하나입니다. 모듈이 없는 디자인을 직접 채택하여 내부 케이블과 구조 부품을 크게 줄이고 배터리 팩의 체적 에너지 밀도를 효과적으로 개선합니다.
배터리 셀이 많을 수록 많은 에너지를 만들 수 있음을 누구나 알고 있습니다. 이론적으로는 숫자만 충분하다면 차량의 배터리 전력을 효과적으로 개선할 수 있지만 여기에는 많은 문제가 따릅니다.
계속해서 맹목적으로 쌓고 싶다면 두 가지 선택밖에 없습니다. 트렁크에 배터리를 채우거나, 캠핑카에 배터리 상자를거리 곳곳에 끌고 다니는 것입니다. 분명히 둘 다 바람직하지 않으므로 문제는 다시 원점으로 돌아갑니다. 즉, 배터리 용량을 더욱 압축하고 밀도를 높이는 동시에 안전하고 안정적인 에너지 밀도 증가를 보장하는 방법을 고민해야합니다.
이 시점에서 업계에는 다양한 기술이 등장하기 시작했습니다.
하나는 Tesla와 Leap가 이끄는 CTC 기술이고 다른 하나는 BYD가 이끄는 CTB 기술입니다.
두 가지 기술적 경로는 동일한 것처럼 보이지만 실제로는 구조와 특정 성능이 다릅니다.
2. CTP vs CTC vs CTB, 어느 것이 더 나을까
먼가 복잡한 것 처럼 보이는데요, 표로 정리해 보겠습니다.
구분 | Module to Pack | CTP | CTC | CTB |
설명 | 셀을 여러 모듈로 나눈 후 장착하는 방식 | 셀을 모듈없이 팩에 직접 통합하는 방식 | 셀을 섀시에 직접 통합하여 차체의 일부로 활용 | 셀을 차체의 일부분으로 통합하는 방식 |
구조적 장점 | 셀 보호 및 모듈 교체가 용이 | 팩 공간 효율성 증가, 경량화 가능 | 경량화 및 구조 통합으로 공간 최적화 | 차체의 일부분이 되면서 공간 활용 극대화 |
공간 효율성 | 공간 활용도가 상대적으로 낮음 | 모듈이 없으므로 셀 에너지 밀도 향상 | 섀시와 통합되므로 더 많은 공간 절약 | 차체와 통합하여 셀 배치 최적화 |
경량화 | 모듈과 팩의 추가적인 무게가 발생 | 모듈 제거로 인한 경량화 | 섀시와 통합으로 무게감소 | 차체 자체가 셀의 보호 역할을 하여 경량화 |
제조 비용 | 복잡한 구조로 인해 제조비용 증가 | 구조 단순화로 비용 절감 가능 | 섀시 제작과 통합에 기인한 제조과정 복잡화 | 차체와 통합하는 고도의 기술이 필요하여 비용증가 |
유지보수 용이성 | 모듈 단위로 유지보수가 가능하여 관리 용이 | 셀 단위로 관리가 필요하여 복잡할 수 있음 | 유지보수 시 섀시 교체가 필요할 수 있음 | 유지보수 시 차체 교체가 필요할 수 있음 |
안전성 | 모듈화로 인해 충격에 강하고 안전성 높음 | 모듈이 없으므로 구조적 안전성확보가 어려움 | 섀시가 셀을 보호하여 구조적 안전성 높음 | 차체와 일체화된 구조로 충격에 강한편 |
열관리 | 모듈 단위로 열관리 가능 | 셀 사이의 공간 감소로 열관리 어려움 | 섀시 통합으로 열 관리시스템 최적화 가능 | 차체와 결합된 열 관리 시스템 구현 가능 최적화 가능 |
에너지 밀도 | 모듈 구조로 인해 상대적으로 낮은 에너지 밀도 | 모듈이 없으므로 에너지밀도 향상 가능 | 섀시와 통합하여 더 높은 에너지 밀도 구현 가능 | 차체와 통합하여 에너지 밀도 최적화 가능 |
3. CTB vs. CTC
1) CTB(Cell-to-Body)가 CTC(Cell-to-Chassis)보다 공간 효율성이 더 좋은 이유
CTC (Cell-to-Chassis): 셀을 자동차의 섀시(하부 프레임)에 통합하는 방식입니다. 이 방식은 셀을 차체 하부에 장착하고 섀시와 일체화해 공간을 절약하며, 셀 밀도를 높일 수 있습니다. 하지만 여전히 셀은 섀시의 하부에 위치하므로 섀시와 차체 내부 공간이 분리되어 있습니다.
CTB (Cell-to-Body): 셀을 자동차의 차체(바디)에 직접 통합하는 방식입니다. CTB에서는 차체 전체가 배터리 공간을 수용하는 구조로 설계됩니다. 이로 인해 배터리 셀이 차체 내부 구조에 더 넓고 깊게 통합될 수 있어, 단순히 섀시에 배터리를 장착하는 CTC보다 더 많은 공간을 활용할 수 있습니다. 차체의 각 부분이 배터리와 밀접하게 통합되기 때문에 공간 효율성이 더욱 극대화되는 것입니다.
2) CTB가 CTC보다 구조적으로 더 강건한 이유
CTC: 섀시가 셀을 보호하는 역할을 하며, 셀과 섀시가 통합되어 구조적 안정성을 높일 수 있습니다. 그러나 섀시가 셀을 품고, 그 위에 차체가 얹히는 구조입니다. 이 경우, 섀시와 차체가 별도로 구성되기 때문에 외부 충격이 섀시를 통해 셀로 전달될 가능성이 있습니다.
CTB: 차체 자체가 셀과 완전히 통합되어 있어, 외부 충격이 들어오면 차체 전체가 배터리 셀을 보호하는 역할을 하게 됩니다. 차체는 차량의 구조적 강도를 유지하는 핵심 요소이므로, 차체와 셀이 일체화되면 충격 흡수 능력이 증가합니다. 이러한 구조적 통합으로 인해 차량의 안전성도 높아질 수 있습니다. 다시 말해, 차체가 셀의 보호막 역할을 하여, 셀을 섀시에만 통합하는 CTC보다 강건한 구조를 만들 수 있습니다.
3) CTB가 고도의 제조 기술이 필요한 이유
CTB(Cell-to-Body) 방식은 셀을 차체의 구조물 자체에 완전히 통합하는 매우 복잡한 설계 및 제조 기술을 요구합니다. 이유는 다음과 같습니다.
차체 설계의 복잡성: 셀과 차체가 완전히 일체화되기 때문에 차체의 강도와 배터리 셀 보호 간의 균형을 맞추는 것이 매우 까다롭습니다. 차체가 배터리를 담는 구조로 설계되어야 하며, 차체의 외형과 배터리의 위치 및 크기가 매우 정밀하게 맞춰져야 합니다. 이러한 복잡한 설계 과정은 고도의 기술을 필요로 합니다.
배터리 셀 통합 및 배치 기술: 셀을 차체와 완전히 결합해야 하므로 배터리 셀의 배열과 통합 기술이 매우 중요합니다. 배터리 팩을 차체에 일체화하면서도 안정적으로 유지되도록 제조 공정이 매우 정밀하게 이뤄져야 합니다.
열 관리 시스템: 차체에 통합된 셀을 효과적으로 냉각하거나 열을 분산시키는 시스템을 설계하는 것은 큰 도전입니다. 차체에 통합된 셀은 열이 고스란히 차체에 영향을 미칠 수 있기 때문에, 이러한 점을 고려한 복합적인 냉각 시스템을 구현해야 합니다.
충돌 안전성: 셀과 차체가 통합된 구조는 외부 충격 시 안전성을 유지하기 위해 고도의 충격 흡수 설계를 필요로 합니다. 차체 전체가 셀을 보호하는 구조이므로 충돌 테스트를 통해 매우 엄격한 안전 기준을 충족해야 합니다.
결론적으로, CTB는 구조적 장점과 공간 효율성이 높지만, 이를 구현하기 위해 고도의 설계, 제조, 통합 기술이 필요합니다. CTC에 비해 더 정밀하고 복잡한 기술이 요구되므로, 생산 비용이 더 높아질 수 있습니다.
'전기차 세부 기술' 카테고리의 다른 글
EUCAR Hazard Levels의 정의 (0) | 2024.09.28 |
---|---|
Wired BMS와 Wireless BMS: 차세대 배터리 관리 시스템의 미래 (1) | 2024.09.27 |
CTB(Cell to Body)와 CTC(Cell to Chassis) 개념 차이 (1) | 2024.09.25 |
전기차 배터리 시스템에서의 저항과 임피던스 개념 (0) | 2024.09.24 |
전기자동차 배터리팩의 최대전압, 에너지 계산 (0) | 2024.09.23 |