고체 전해질 배터리 대량 생산의 현주소: 2027년까지 넘어야 할 5대 장벽과 글로벌 경쟁 구도
2025년 현재 전기차 시장은 연간 3,500만 대 규모로 성장했으며, 배터리 기술 경쟁의 핵심은 에너지 밀도와 안전성으로 좁혀지고 있습니다. 고체 전해질 배터리(SSB)는 이 두 가지 문제를 동시에 해결할 수 있는 차세대 기술로 주목받으며 전 세계 주요 기업들이 사활을 걸고 있습니다. 그러나 기술적 난제와 생산 비용 문제로 인해 본격적인 상용화는 아직 요원한 상황입니다.
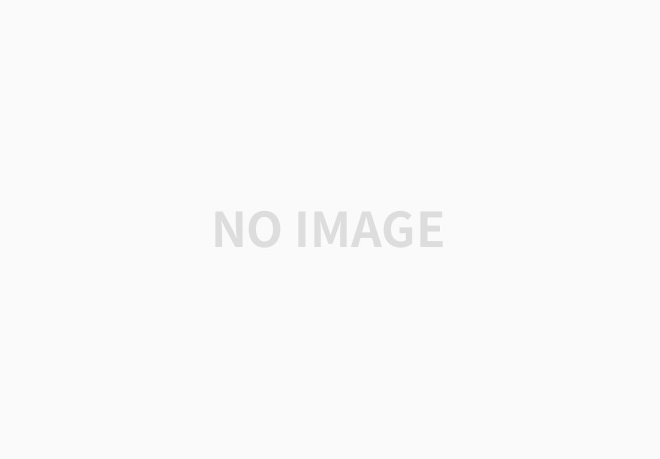
■■ 기술적 도전과 생산 현황 분석
현재 고체 전해질 배터리의 최대 에너지 밀도는 500Wh/kg 수준으로, 기존 리튬이온 배터리(250Wh/kg) 대비 2배 이상의 성능을 보입니다. 삼성SDI가 개발한 프로토타입의 경우 1회 충전 시 800km 주행이 가능하며, CATL은 2024년 500Wh/kg 급 배터리 시제품 공개를 통해 기술력을 과시했습니다. 그러나 이러한 수치는 실험실 환경에서의 결과일 뿐, 양산 단계에서는 350Wh/kg 수준으로 하락할 것으로 예상됩니다.
주요 기술 경로별 생산 효율을 비교해보면 황화물계 전해질이 85%의 이온 전도율로 가장 우수하지만, 습도에 약해 생산 환경 관리 비용이 kWh당 $12 추가 발생합니다. 반면 산화물계는 내구성이 뛰어나지만 제조 공정 중 1,000°C 이상의 고온 소결이 필요해 에너지 소비량이 30% 증가하는 문제점을 안고 있습니다.
■■ 글로벌 기업별 양상 전략
유럽에서는 프랑스의 블루솔루션(Blue Solutions)이 1997년부터 폴리머 기반 SSB를 연간 1.5GWh 규모로 생산 중입니다. 주로 전기 버스에 공급되며, 2026년부터는 승용차 시장 진출을 목표로 2세대 기술 개발에 박차를 가하고 있습니다. 영국의 일리카(Ilika)는 2025년 2분기 말까지 1.5GW 규모 생산라인 가동을 앞두고 있으며, 타타 그룹과 협력해 2026년 상용차 양산 체계를 구축할 계획입니다.
미국 스타트업 퀀텀스케이프(QuantumScape)는 폭스바겐 그룹과 협력해 2028년까지 셀당 $100 미만의 가격 목표를 설정했습니다. 40Ah 규모 셀의 경우 800회 사이클 후 용량 유지율 90%를 달성했으나, 두께가 85mm에 달해 차량 적용 시 공간 효율성 문제가 남아 있습니다.
중국 기업들의 움직임은 특히 주목할 만합니다. BYD는 2024년 60Ah 전고체 배터리 파일럿 생산을 시작했으며, 2027년 시험 생산량을 5GWh까지 확대할 계획입니다. CATL은 1,000명 이상의 전담 R&D 인력을 투입해 황화물계 SSB 개발에 집중하고 있으며, 2027년 소량 생산을 목표로 공장 건설에 착수했습니다.
■■ 고체 전해질 배터리(SSB) 기술 경로별 핵심 공정 과제 분석
2025년 현재 고체 전해질 배터리 개발은 폴리머(Polymer), 황화물(Sulfide), 산화물(Oxide) 세 가지 주요 기술 경로로 구분되어 진행 중입니다. 각 기술별 특성에 따른 생산 공정의 차이는 제조 효율성과 상용화 가능성을 결정짓는 핵심 변수로 작용하고 있습니다.
■ 폴리머 기반 SSB의 열적 한계와 EV 적용 도전
폴리머 전해질은 50~80°C의 고온 환경에서 최적 이온 전도도(10⁻⁴~10⁻³ S/cm)를 달성합니다. 이는 분자 사슬 구조가 가열 시 유연해지며 리튬 이온 이동 경로가 확장되기 때문입니다. 프랑스 블루솔루션의 경우 1997년부터 연간 1.5GWh 규모로 폴리머 SSB를 생산 중이지만, 전기 버스 등 지속 가동 시스템에 한정 적용되고 있습니다. 승용차 적용 시 주차 중 배터리 온도가 실외 온도(-20°C~40°C)로 변동할 경우 성능이 60% 이상 저하되는 문제가 발생합니다.
제조 공정에서 폴리머/리튬금속 계면 접합을 위해 150°C 이상의 열압착(thermal lamination) 공정이 필수적입니다. 이 과정에서 발생하는 0.5~1.2%의 열수축 불균형은 전극 박리 현상을 유발하며, 이를 보정하기 위해 3차원 메시 구조의 금속 집전체를 적용해야 합니다. 결과적으로 셀 에너지 밀도가 이론치(500Wh/kg) 대비 35% 감소하는 주요 원인으로 작용합니다.
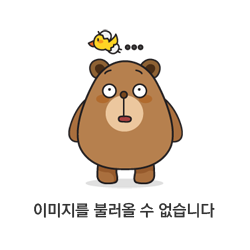
■ 황화물 기반 SSB의 습도 관리와 덴드라이트 문제
황화물 전해질은 25°C 기준 10⁻² S/cm 이상의 우수한 이온 전도도를 자랑하나, 공기 중 500ppm 이상의 수분 노출 시 분해 반응으로 황화수소(H₂S)가 발생합니다. 이로 인해 생산라인 전체를 0.1% 이하의 초건조 환경(露點 -60°C)으로 유지해야 하며, 진공 챔버 구축 비용이 kWh당 $12 추가됩니다. CATL의 2024년 시제품은 황화리튬(Li₃PS₄) 전해질에 나노 실리콘 코팅층을 적용해 수분 차단 성능을 85% 개선했으나, 양산 단가가 기존 대비 220% 상승하는 trade-off가 발생했습니다.
충전 시 리튬 덴드라이트 성장 문제는 황화물 SSB의 치명적 약점입니다. 0.5mA/cm² 전류 밀도 조건에서 100사이클 후 50μm 길이의 덴드라이트가 관찰되며, 이는 고체 전해질 내부 균열을 유발해 단락 사고 위험을 3배 증가시킵니다. LG에너지솔루션은 2024년 유전체 강유전체 물질(BaTiO₃)을 전해질 표면에 50nm 두께로 코팅해 덴드라이트 성장 속도를 70% 억제하는 데 성공했으나, 공정 시간이 35% 연장되는 문제가 남아 있습니다.
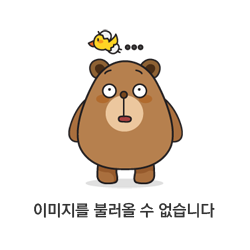
■ 산화물 기반 SSB의 고온 소결과 계면 저항 과제
산화물 전해질(예: LLZO, Li₇La₃Zr₂O₁₂)은 1,000°C 이상의 고온 소결(sintering) 공정을 통해 95% 이상의 결정화도 달성이 필수적입니다. 닛산의 2023년 시험라인 데이터에 따르면, 1,250°C에서 12시간 소결 시 10⁻⁴ S/cm의 이온 전도도를 얻을 수 있으나 에너지 소비량이 기존 리튬이온 배터리 대비 1.8배 증가합니다. 도요타는 2025년 마이크로파 소결 기술 도입으로 공정 온도를 800°C로 낮추고 시간을 4시간으로 단축했지만, 5% 포어(void) 발생으로 인해 계면 접촉 면적이 78%로 제한됩니다.
산화물/음극 계면 저항은 300Ω·cm² 수준으로 황화물(50Ω·cm²) 대비 6배 높습니다. 삼성SDI는 2024년 음극 표면에 Li₃BO₃ 계층을 100nm 두께로 증착해 저항을 40% 감소시켰으나, 이차전지 전체 에너지 밀도를 15% 희생해야 했습니다. 보쉬의 2025년 솔루션은 전해질 입자를 50nm 크기로 분쇄해 표면적을 5배 증가시킴으로써 접촉 저항 문제를 해결했지만, 나노 분말 제조 비용이 기존 대비 320% 급등하는 경제적 타협이 필요했습니다.
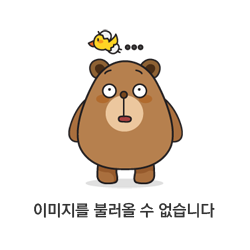
■ 종합 기술 경쟁력 평가 지표
<생산성 측면> 황화물계는 냉간 압착 공정으로 15분/셀 처리 가능한 반면, 산화물계는 고온 소결로 8시간/셀 소요됩니다. 폴리머계는 열압착 2시간 필요하지만 후공정 통합도가 높아 전체 라인 효율이 85%로 가장 우수합니다.
<에너지 효율> 산화물계 소결 공정에 전체 에너지의 62%가 집중되며, 황화물계는 습도 제어시설이 전체 전력의 45%를 소모합니다. 폴리머계는 열관리 시스템이 30%의 추가 전력을 요구합니다.
<안정성> 황화물계 수명이 500사이클(용량 80%)로 가장 짧으며, 산화물계 1,200사이클, 폴리머계 800사이클 순입니다. 충전 속도는 황화물계가 3C-rate로 가장 빠르나, 산화물계 1.5C-rate, 폴리머계 0.8C-rate로 제한됩니다.
이러한 기술적 난제를 극복하기 위해 2025년 현재 글로벌 기업들은 하이브리드 전해질 시스템 개발에 주력하고 있습니다. 도요타는 황화물-산화물 다층 구조 전해질을 적용해 이온 전도도 2×10⁻³ S/cm 및 공기 안정성 48시간 달성에 성공했으며, LG에너지솔루션은 폴리머-황화물 복합 전해질로 -30°C 저온 성능을 개선했습니다. 각 기술 경로의 고유 장점을 융합한 접근법이 2027년 대량생산 체계 구축의 핵심 과제로 부상하고 있습니다.
■■ 국가별 생산 역량 비교
일본은 1,300건 이상의 특허를 보유한 도요타가 선두에 서 있습니다. 2027년 양산 목표로 설정한 도요타의 SSB는 10분 충전으로 1,000km 주행이 가능하며, -30°C에서도 성능 저하 없이 작동하는 것이 특징입니다. 닛산은 2029년 상용화 예정인 배터리의 제조 단가를 기존 대비 20% 절감하는 데 성공했으며, 2030년까지 생산량의 30%를 해외 공장으로 이전할 계획입니다.
한국의 경우 삼성SDI가 2023년 완공한 세계 최대 규모의 SSB 파일럿 라인(연간 0.5GWh)을 운영 중입니다. 2025년 3월 기준 500Wh/kg 프로토타입 개발을 완료했으며, 2027년 상용화를 목전에 두고 있습니다. LG에너지솔루션은 2024년 12월 충전 속도 10배 향상 기술을 개발해 주목받았으며, 2028년까지 폴리머-황화물 복합 전해질 양산 체계 구축에 총 5조 원을 투자할 예정입니다.
중국의 산업화 속도는 가히 경이적입니다. 2025년 2월 중국전기차100인회 발표에 따르면, 2027~2028년 SSB 산업화 본격화와 2030년 연간 100GWh 생산 능력 달성을 목표로 하고 있습니다. 상하이자동차(SAIC)는 2027년 SSB 탑재 차량 출시를 공식화했으며, 이 배터리의 에너지 밀도는 400Wh/kg에 달합니다.
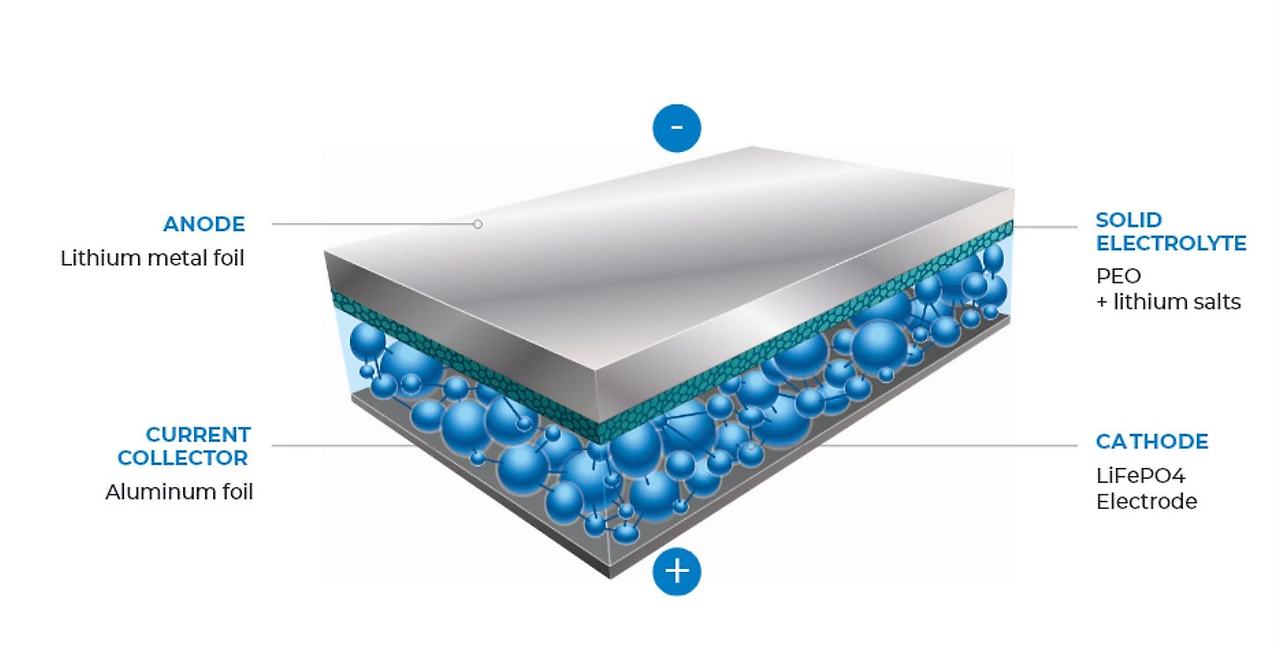
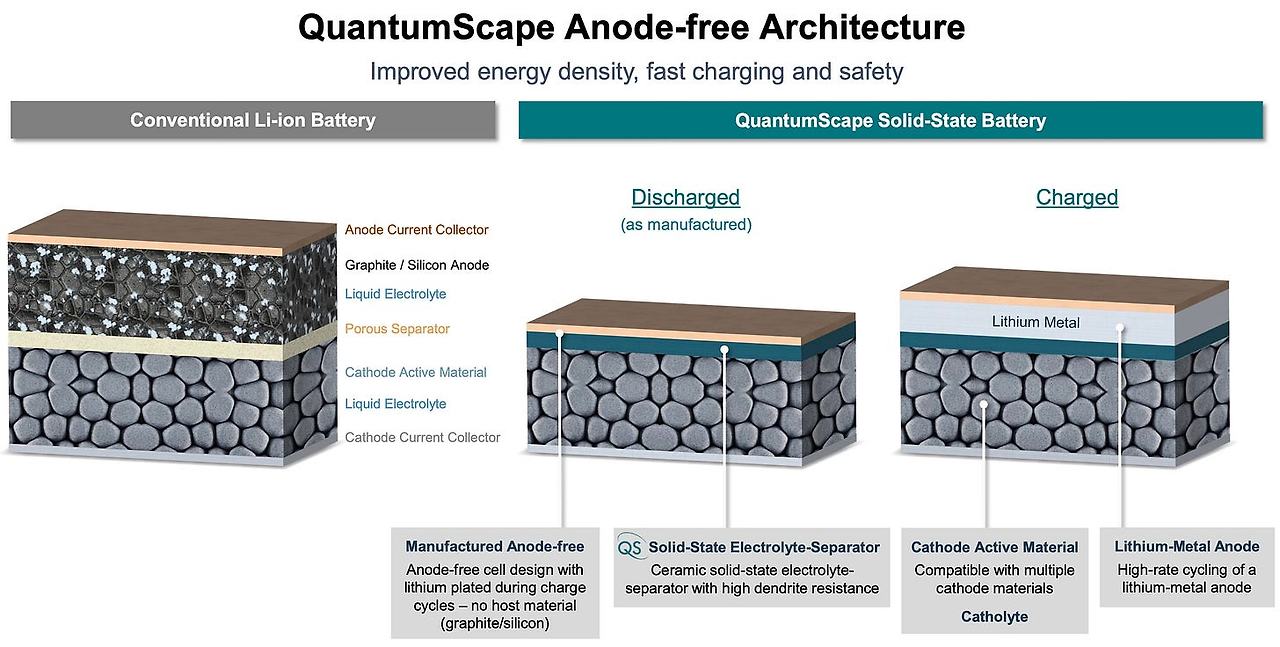
■■ 향후 5년 간 주요 과제
첫 번째 장벽은 원재료 공급망입니다. 리튬 메탈 양산을 위해 전 세계적으로 2027년까지 25개의 새로운 광산 개발이 진행 중이지만, 현재 확보된 자원량은 예상 수요의 40%에 불과합니다. 두 번째로 생산 장비 개발 지연이 문제입니다. 진공 환경에서의 전극 적층 공정에 필요한 장비의 경우, 2025년 현재 독일 Manz사가 개발한 장비가 시간당 10셀 처리 능력을 보이지만 양산 요구치인 시간당 100셀 처리에는 도달하지 못했습니다.
세 번째로 수명 문제가 남아 있습니다. 1,000회 충전 사이클 기준 용량 유지율 80% 달성을 위해 황화물계 전해질은 2024년 750회, 산화물계 900회 수준에서 기술 개발이 진행 중입니다. 네 번째 과제는 열 관리 시스템입니다. 고체 전해질의 경우 작동 온도 범위가 60~80°C로 제한되어 있어, 별도의 냉각 시스템 추가로 인해 배터리 팩 무게가 15% 증가하는 문제가 발생합니다.
마지막으로 경제성 확보가 최대 난제입니다. 2025년 1분기 기준 SSB 셀 제조 단가는 kWh당 $180으로, 리튬이온 배터리($70/kWh) 대비 2.5배 이상 높습니다. 보스턴컨설팅그룹(BCG) 분석에 따르면 2027년이 되어야 $100/kWh 이하로 하락할 것으로 전망됩니다.
■■ 산업계 전망과 향후 과제
2030년 글로벌 SSB 시장 규모는 600억 달러에 달할 것으로 예상됩니다. 이 중 45%를 중국 기업이 차지할 것이며, 유럽 25%, 한국 15%, 일본 10% 순으로 예측됩니다. 특히 항공우주 분야 적용이 주목받아, 2028년 예정된 보잉 787 SSB 시험 비행 성공 시 항공기 연료 비용의 30% 절감 효과가 기대됩니다.
최종적으로 2027년은 SSB 산업의 판도를 가를 중요한 분기점이 될 것입니다. 기술 선도국과 후발주자 간 경쟁이 더욱 가열되는 동시에, 기존 리튬이온 배터리 업체들의 사업 전환 압력도 극대화될 전망입니다. 이 과정에서 생산 효율성 제고와 원가 절감을 동시에 달성한 기업만이 최종적인 생존자로 남을 수 있을 것입니다.
다녀가신 흔적은 아래의 하트 모양의 공감 (♥)을 눌러서 남겨주시길 부탁드립니다.
로그인하지 않으셔도 공감은 가능합니다.
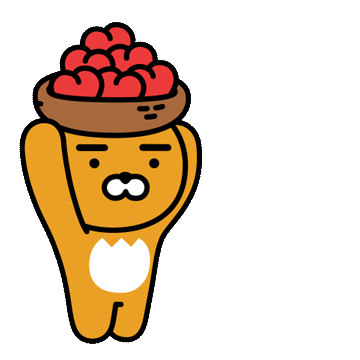
감사합니다 !
'전기차 세부 기술' 카테고리의 다른 글
LFP 배터리의 OCV 평탄화 원인 및 주요 배터리 유형별 SOC 커브 특성 분석 (0) | 2025.03.05 |
---|---|
확산 계수(Diffusion coefficient)가 배터리 관리 시스템(BMS) 개발에 활용되는 메커니즘과 기술적 적용 사례 (0) | 2025.03.04 |
인터배터리 어워즈 2025 (2) | 2025.02.28 |
청화대학교 장강 실험실 (0) | 2025.02.27 |
GM 울티엄 배터리의 혁신: 무선 BMS 기술이 이끄는 전기차의 미래 (1) | 2025.02.23 |